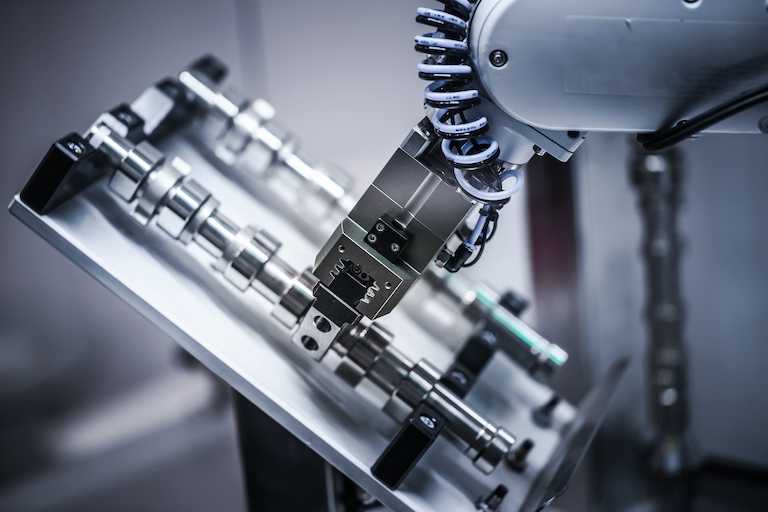
From location analysis to process optimization:
how Group-IPS is helping clients build the factories of the future
Finding the ideal location for a new factory, defining the investment requirements and risks, designing and organizing the right layout for extracting the most value from operations, developing and optimizing improved productivity manufacturing processes - these are just a few of the tasks industrial and investment companies all over the world face daily. The question is how to execute them now, while ensuring the changes stand the test of time from the competitivity, financial, and sustainable perspectives. The key to success, we believe, is looking at the business case specifics together with the technicalities of the factory as a whole.
At Group-IPS, we help clients achieve their projects from the very first spark of inspiration to the final moment of production. Our teams cover the process of building a new facility long before actual construction begins. Other specialists focus on optimizing processes for new and existing factories; we put everything in context, add a pinch of the newest trends, with an emphasis on sustainability and the specific impact of the project. That’s how we are helping to build the factories of the future for companies all over the world.
Search for the right plot
When looking for the perfect location of a new facility, we scan the market for potential sites, analyse logistics networks and optimized paths, evaluate locations from a socioeconomic point of view, prepare technical due diligences, and prepare the investment and projects masterplan including risk analysis on schedule, market evolution and conditions and potential permitting challenges.
Our clients get a comprehensive investment decision report covering all angles that matter to the business case, investors, and stakeholders to support an informed decision based on the right combination of data analytics and experience. Once investment is approved, we protect the investor by maintaining our involvement in the project throughout KPIs continuous monitoring while our EPCM specialists help to materialize the plans.
Growing without expanding
One of our clients producing specialized industry equipment was looking for analysis of their operations for improving production without major investment. The current factory was producing 14,500 units a year. After evaluating different production and logistics scenarios, we concluded that the capacity could be increased up to 52,000 units a year in the same factory.
Finding ways to grow on the current site
A new plant is not always the best alternative. We seek the most profitable options for our customer including investing in an upgrade or enlargement of current facilities after performing an analysis of current processes in existing facilities. With the latest technologies, we can find ways to maximize production efficiency and internal and external logistics processes. Our analysis always includes a financial profitability analysis (ROI, NPV, Payback period, etc.) and complete information on the risks and benefits including environmental, social, and future adaptation for climate change.
Our methodology for researching new manufacturing processes:
In depth analysis of the raw materials and product to be produced via our Product2Manufacturing scale-up study to determine the feasibility of the project.
Process conceptual design to enable further optimization.
From a micro to macro manufacturing process scale we build pilot-project lines testing actual materials and finished products.
Once the Pilot plant phase is commissioned, qualified, and verified, we continue with the manufacturing size EPCM phase.
Innovation in production waste utilization
Nowadays, a competitive edge is not only driven by efficient operations, but also business resiliency and adaptation to the sustainability challenges of the future. All industrial fields can benefit from finding new uses for co-products that would otherwise be discarded. Together with the client, our technical experts research innovative techniques to improve production and extract value from anything and everything that enters the manufacturing site. These improvements help raise efficiency at the factory while also making it more resilient to supply chain disruptions and environmental regulatory risks while also less dependent on global material price swings targeting always to bring waste to zero, whether that’s in the food & beverages industry or steel production.
Reducing waste of raw materials
Let’s have a look at the example of company processing fruits. During eight weeks, we analysed processes in the factory, its layout, and possibilities for improvement. Our analysis showed the client has 36 % potential for their OEE improvement and after another improvements saved 21% of water consumption.
These are just a few examples of what our Predict & Innovate business unit can help you with. We are ready to support you in all dimensions of your projects, building on our technical expertise and experience while being mindful that your investment needs to tell the right financial, social, and sustainability story. Our innovative skills, sustainable processes, and environment services include gathering data, handling operations, developing and testing products as well as technology. Just ask us how we can help future-proof your factory.
Contact details
Carlos Bravo Fernandez
E: carlos.bravo.fernandez@group-ips.com
T: +34 663 861 551