Group-IPS develops new filling line facility for Hoegaarden:
Creative solution from project management to architecture
AB InBev
In 2018, AB InBev, manufacturer of the world-famous Belgian beer Hoegaarden, approached Group-IPS with a request to come up with the best location and layout for a new can filling line. From masterplan, through project management, to architecture, and engineering, we had to find new ways to satisfy the business needs as well as meet specific requests from the municipal authorities and locals. Not only did we manage to meet the first sellable product deadline, but we also delivered a future-proof facility with aesthetic architecture reminiscent of the signature glass of Hoegaarden.
Project Location
Altenaken, Belgium
Status
Finished
Budget
52 mil. €
Year
2018-2020
The existing production facility of Hoegaarden is synonymous with the village itself. The requests were for the new factory to have positive visual impact on the surrounding landscape.
Finding the right location
AB InBev planned to build a new filling line to increase their capacity for canned beer production in Belgium. Initially, Group-IPS’s task was to find suitable locations and prepare the masterplan. We created a “reference masterplan” – the ideal layout of the facility without knowing the exact site for its placement, together with cost estimate and time schedule. After detailed research, we recommended the existing Altenaken site as it checked all the boxes: logistic-, land- and cost-wise. However, expansion of the current facility was not without constraints.
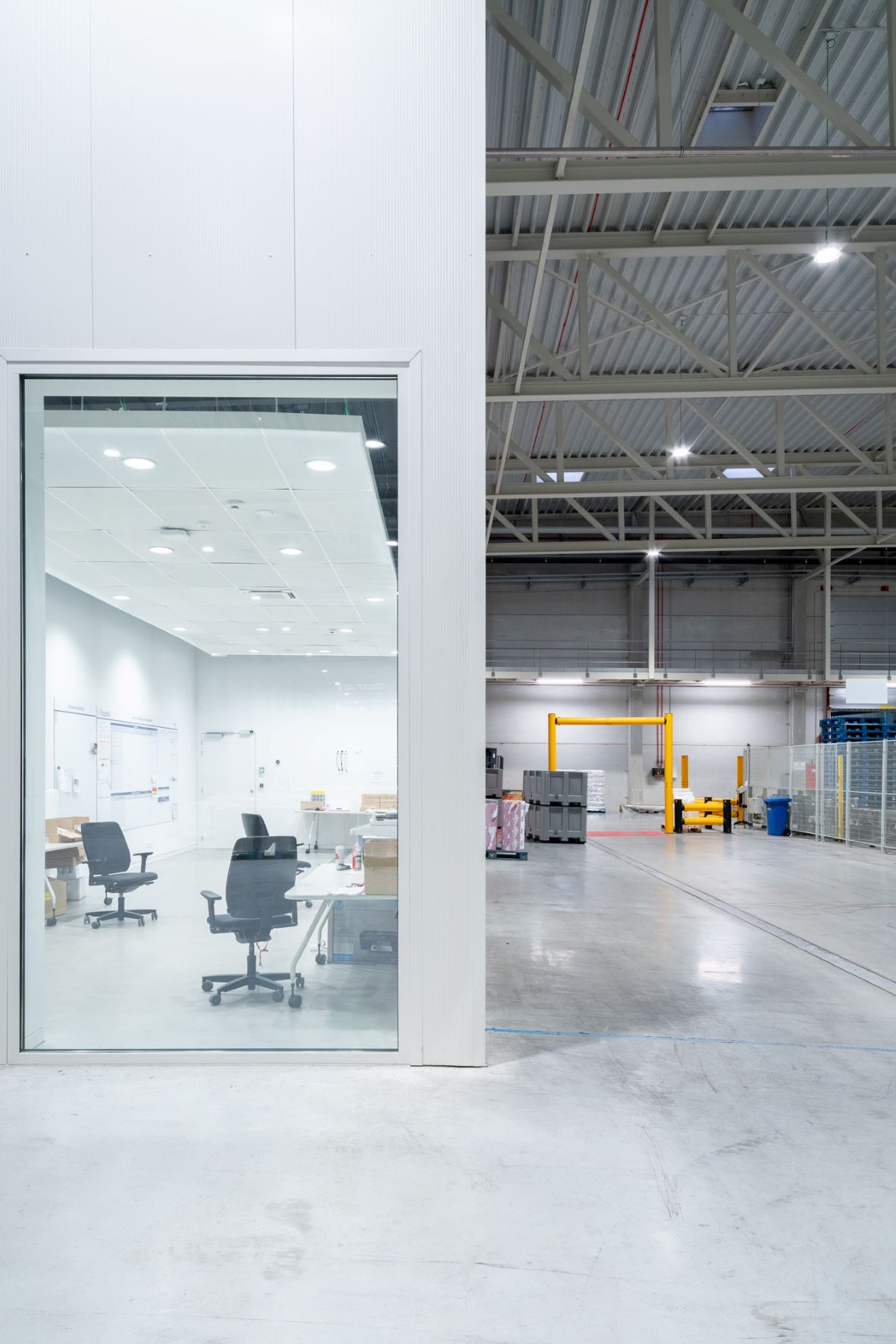
Identifying risks
The existing production facility of Hoegaarden is synonymous with the village itself. The requests were for the new factory to have positive visual impact on the surrounding landscape. Some key constraints had to be taken into account:
- Location. We had to negotiate with both regional municipalities in Belgium.
- Logistics concept. A can filling line is a mixture of production and warehousing, so we had more stakeholders and had to define logistics perfectly.
Here we utilized the extensive knowledge and experience of our strategic consultants and digital supply chain department.
Because the project involved beer production, we also had to take into special consideration the layout of the expanded facility, particularly the windows placement, to avoid undesirable temperature shocks.
The final risk we identified from the beginning was that this expansion of an existing facility would not allow for any halt in the production processes in the building. Our goal was to secure the logistics for construction as well as maintain production throughout the entire process.
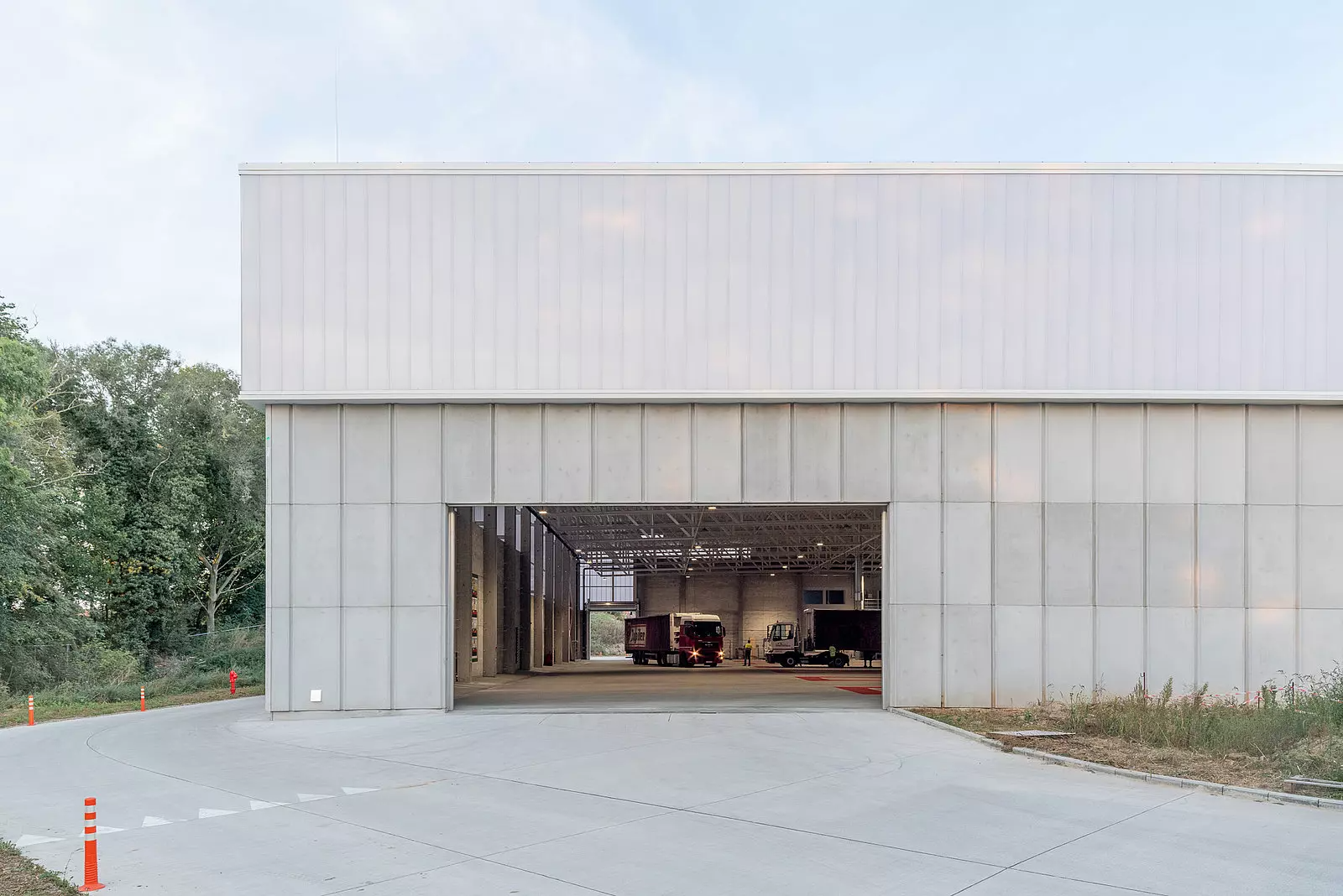
Our Approach: Integrated Project Delivery – shortening project time to a minimum
The new facility was to be established on the existing area used for logistics, meaning the loading docks would be blocked. Therefore, we initiated the concept of a phased masterplan and construction. We defined parts of the building that were to be finished first and could be used for logistics, and then shuffled the sequences/processes as necessary over time according to the progress of the construction. We did all of this to ensure production wasn’t halted or slowed.
This was not the only highly specific aspect of the project. Usually, we would define the detailed scope, layout and budget of the project, validate it with the client, execute the procurement strategy, and then begin construction. However, when we had to begin building in order to ensure delivery of the facility would be on time, the design was not finalised, meaning we could either finish the design (and procurement) and delay construction, or we could begin construction without having full information on the final building design. We chose the second way to ensure our client would have their facility on time.
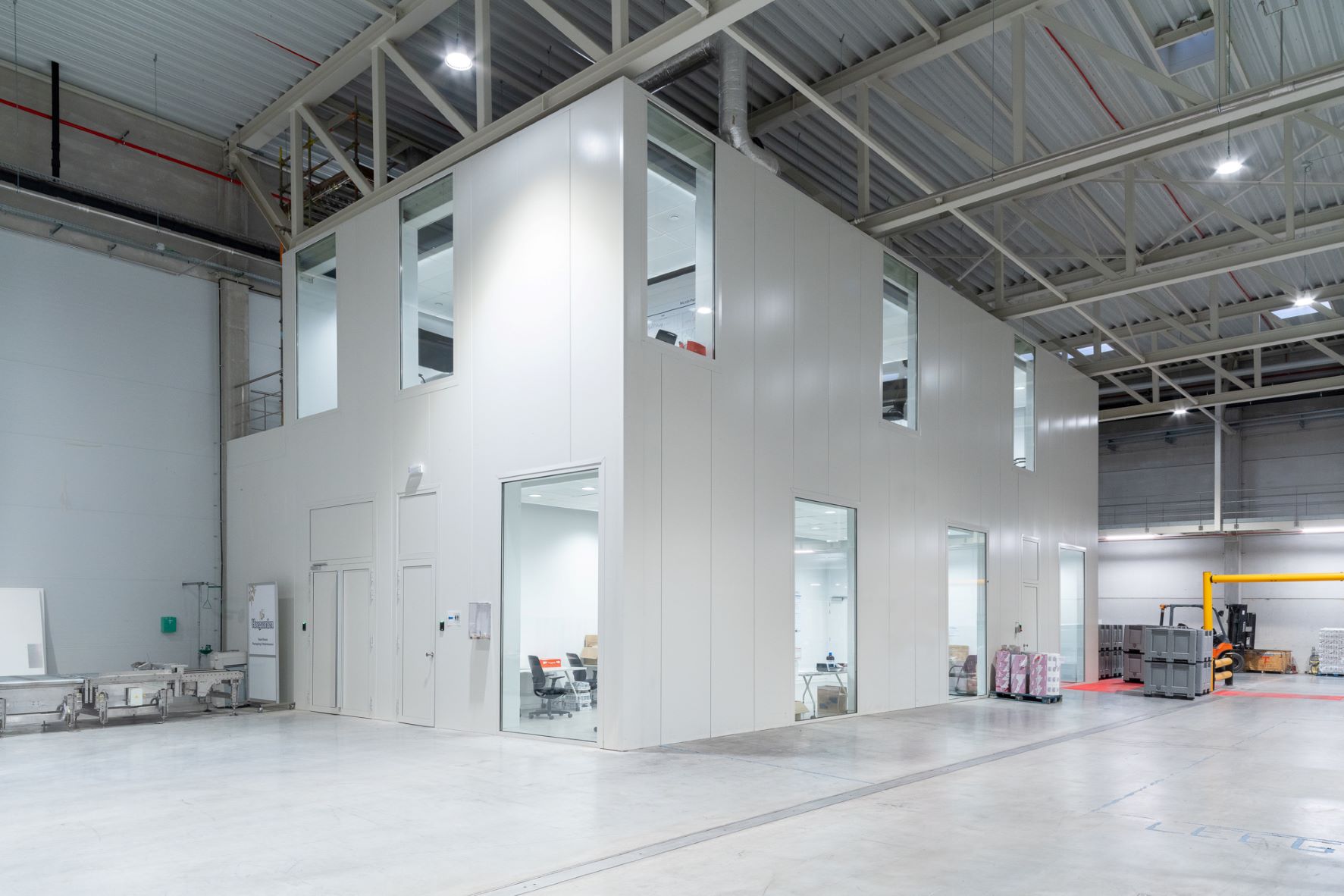
We developed and introduced an approach called integrated project delivery where we created the concept design (including lookalike and structure of the building) and fixed the guaranteed maximum price (GMP) with the general contractor. We worked on detailed design together with the contractor progressively whilst controlling its quality, ensuring the design met the clients’ strict requirements and requested standards.
Our procurement department managed to agree on a GMP with other suppliers, too, meaning the budget was set and could only go lower (which we managed to do during the design/construction period). Through this approach, we saved approximately three months of time, but it would not have been possible without the close cooperation between IPS professionals, the client and the contractors.
The design of translucent anti-glare polycarbonate panels, white sandwich panels and small cantilever over the concrete panels resembles the foam bubbles and replicates the head at the top of the glass.
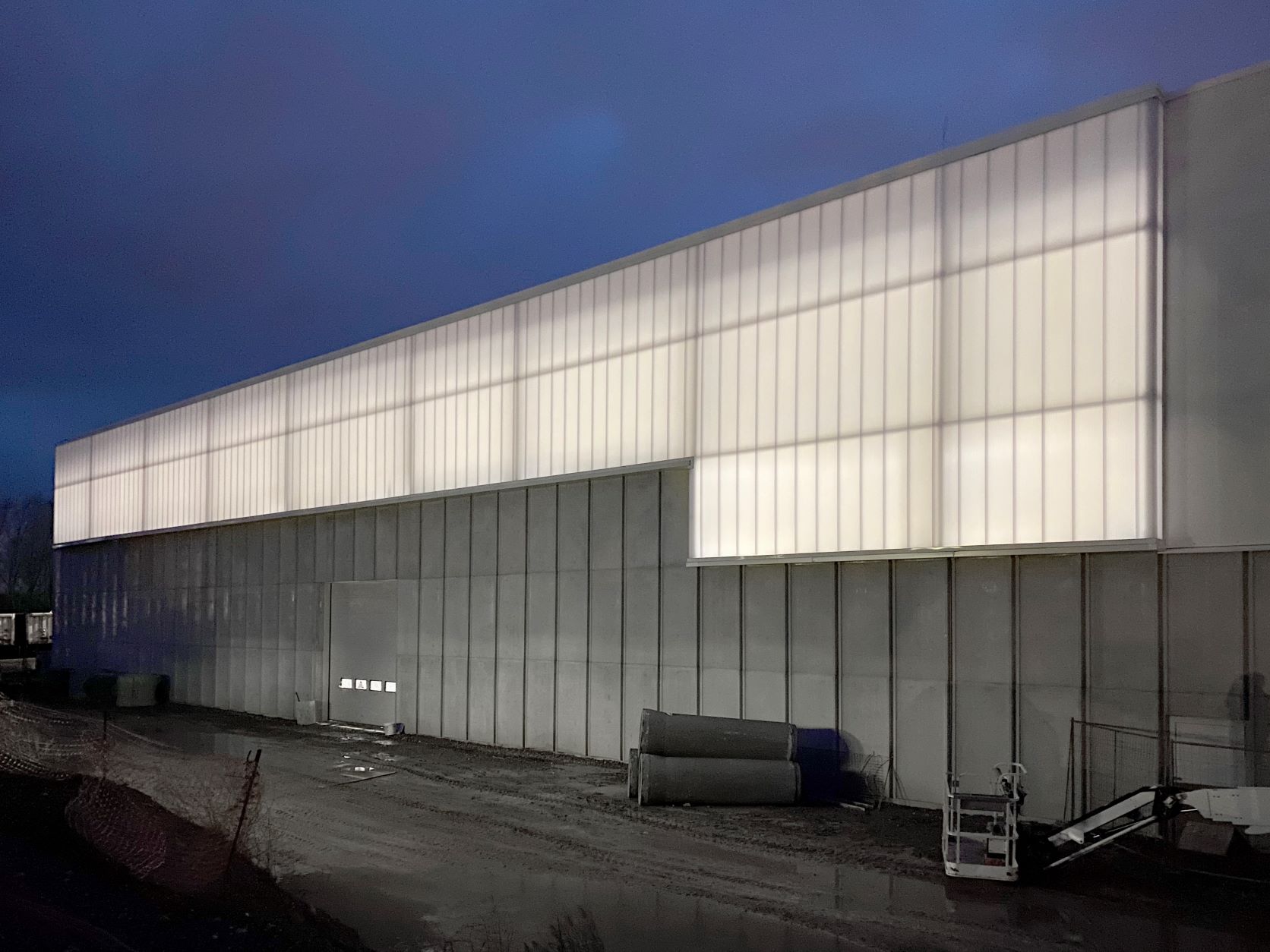
The Architecture – a tribute to the signature glass
Located directly in the village, surrounded by bicycle paths and also open for visitors, the AB Inbev Hoegaarden factory is an integral part of the local landscape. The expansion of the facility, therefore, needed to blend into the surroundings and the facade became a particularly important point of design. It was designed using the combination of concrete, sandwich panels and polycarbonate, and is reminiscent of the brand’s iconic glass.
The design of translucent anti-glare polycarbonate panels, white sandwich panels and small cantilever over the concrete panels resembles the foam bubbles and replicates the head at the top of the glass. Meanwhile, the concave shape of the concrete panels represents the beer glass itself. The architecture makes the project even more special and shows also that industrial design can be visually appealing.
The Result
AB InBev chose Group-IPS for its strong mix of strategic consulting, engineering, procurement and project management services (epcm). From the first spark of inspiration for a new filling line, to finding the right location, to the final building and equipment commissioning and handover, we used all our experience to develop new approaches that ensured the project was successful.
We delivered the masterplan and superb architectural design. We managed the procurement and construction in record time thanks to our approach, and direct and honest communication. Everyone in the existing facility was affected by the construction, yet everyone cooperated in a professional manner; IPS, AB InBev and the contractor teams worked as one for the entire length of the project. We instilled confidence that the project would be finished on time and on spec, delivering not just a facility ready for the current requirements, but one that would also meet future ones. For example, the packmat roof’s loading is suitable for use as a floor in case further expansion is needed, and there are many other features that make the new factory adaptable for whatever the future brings.